Marine sector embraces new initiatives in 3D printing
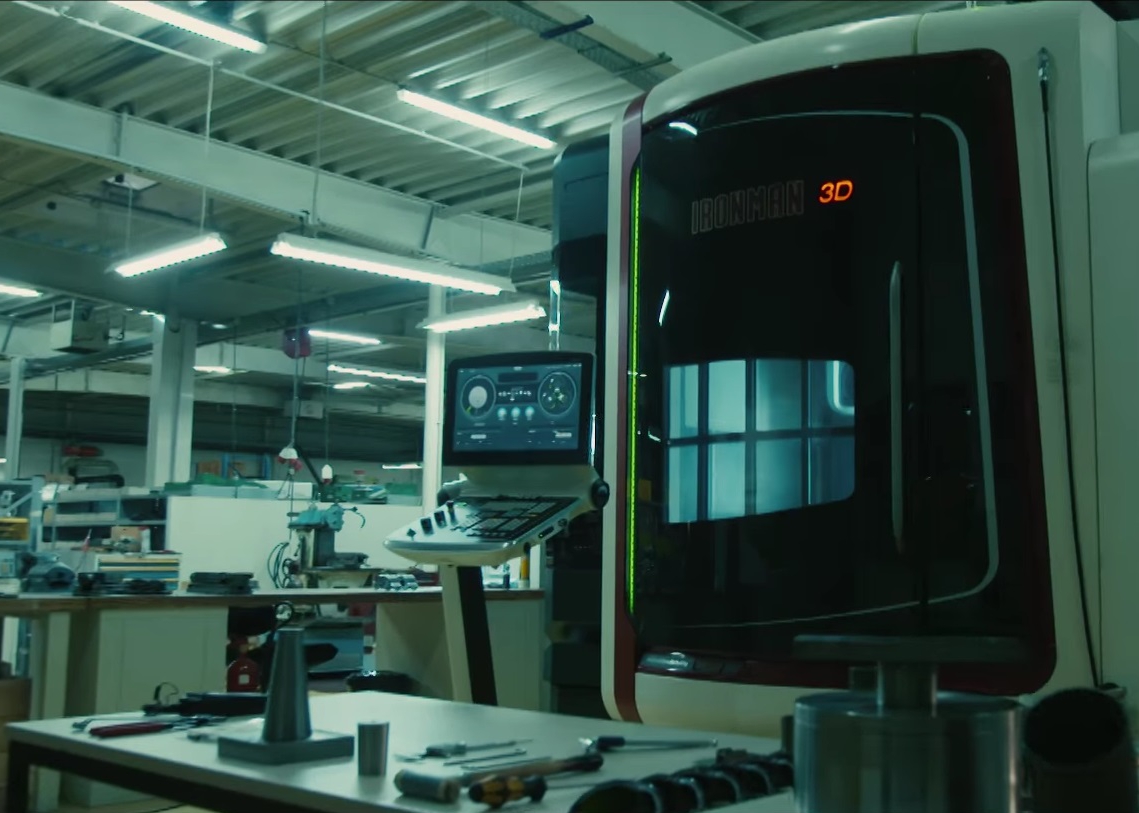
Additive manufacturing, or 3D printing, is taking firm hold in many industries. Projects in the marine field, albeit relatively few, show the participants’ determination to be prepared for the future. David Tinsley reports.
3D printing is rapidly becoming a practical tool that looks set to reshape production and manufacturing. It confers the ability to manufacture according to a specific set of digital instructions, allowing products to be constructed at will and to high levels of customisation. However, it also introduces new challenges in terms of technical complexity and data demand, and calls for significant capital investment.
The process of 3D printing (3DP) or additive manufacturing (AM) is less wasteful in material requirement than conventional manufacturing, and offers considerable time savings and logistic benefits. 3D printers deposit thin layers of material to create a component or product by following a digital blueprint.
It inverts the custom die manufacturing process, changing it from subtractive to additive. The whittling down of metal to the required size and form is replaced by a CAD (computer-aided design) file-controlled, layer-by-layer build-up of material.
The automotive and aircraft manufacturing industries are currently among the most active practitioners of AM/3DP techniques. From its initial main use in prototyping, the technology has rapidly advanced and evolved and is being increasingly employed in the production process.
For example, GE Aviation is using AM/3DP in the manufacture of a new jet engine fuel nozzle. Instead of being made in conventional manner from 20 different parts, it is produced in a single stage with a 3D printer, said to be 25% lighter and five times more durable than the conventional product. Recourse is made to Big Data and data analytics to ensure product quality, by monitoring and analysing the process and parts during the laser sintering process.
Widening application of the technology across the componentry range is such that GE Aviation forecasts the manufacture of some 100,000 additive parts by 2020. Boeing is also reported to be using multiple, AM-derived components in the production of its new 787 Dreamliner aircraft.
Airbus has opened its first manufacturing facility for 3D printing of complex titanium components in Germany. The company stated that “3D metal printing....will not replace our tried and tested processes, but it opens up as yet almost incalculable potential for us, especially when it comes to production times, flexibility in production, and the weight of the components.” Elsewhere in industry, aluminium producer Alcoa is using 3DP to make custom dies for casting nickel alloy engine parts able to withstand extremely high temperatures.
Uptake accelerating
The commercial marine sector has, until very recently, been slow in investigating the opportunities presented by AM/3DP, although the AP Möller-Maersk Group has implemented 3DP on tankers, to gain insights into the practical use of the technology and obtain feedback from crew. The US Navy has also been trialling 3DP at sea on capital ships since 2014. In addition, shipbuilders in South Korea, the USA and China have launched AM/3DP projects.
Several major industrial groups which have a stake in the marine market, including GE, are planning mass production of parts for other sectors using AM/3DP. Rolls-Royce, with its extensive interests in the production of ships’ machinery and equipment in Europe and South America, has secured EU funding to research the potential for 3D printers in making aero engine components.
An important development in a maritime industries’ context was the study ‘3D Printing of Marine Spares’ completed in early 2016 by a broad church of Dutch interests. This has led to a further, pragmatic initiative within the port of Rotterdam, which is laying the foundations for a digital manufacturing infrastructure.
One fundamental constraint in any form of laser-based manufacturing is the exponential increase in costs relative to the size or build area of the part to be made. It therefore seems inconceivable, in the foreseeable future at least, that AM will be used for major steel structural work. However, the technology clearly holds potential in the shipbuilding and marine equipment fields for the production of smaller parts or elements and/or for small series runs, by obviating tooling and set-up costs.
The world’s two largest shipyards, Hyundai Heavy Industries and Daewoo Shipbuilding & Marine Engineering, have been investigating 3DP for some time, and by 2015 had already identified 15 major ship parts suitable for the process. It was suggested last year that this figure could rise to 165 parts by 2018. The investments that are currently being made in South Korea at large in the development of the technology for application to industrial production suggest that the country may emerge as a leader in this field.
Spare part printing
For the marine industries, AM/3DP appears to offer the greatest prospects right now in the creation of spare parts for maintenance and repair (M&R), which accounts for a substantial proportion of vessel operating budgets. Through the printing of parts onboard, or at a facility in the ship’s next or forthcoming port of call, the technology could reduce M&R costs by cutting shipboard inventories and realising logistical benefits, especially for vessels with complex trading patterns.
Although many parts are surely beyond the scope of onboard printing, the potential presently extends to some of the most commonly required and smaller replacement parts, including valves, pump components, tubes and pipes. For an urgently-needed or critical part where the 3DP-generated equivalent could not meet long-life guarantee criteria, an interim-use part could be immediately printed, offering a service life of at least a few hundred operating hours until the requisite, conventionally manufactured component is delivered and fitted.
The high initial cost of 3DP equipment has to be weighed against the printer’s flexibility for immediate detail changes and minimal wastage of expensive material plus logistic benefits with regard to spares sourcing and delivery. In the case of onboard 3DP, a limiting factor may be the volume of data necessary for transmitting to the ship to build the requisite component using the CAD-derived three-dimensional file.
A seminal project was completed in the Netherlands at the end of December last year to investigate the viability of making spare parts for ships using 3D printing technology. Launched by the South Holland regional development agency InnovationQuarter, the Port of Rotterdam Authority, and RDM Makerspace, the pilot project involved collaboration by 28 companies and organisations, including Keppel Verolme (shiprepair), Huisman (crane manufacture), MARIN (marine technical research), and Broekman (logistics), plus firms from other industrial sectors, such as Fokker (aerospace) and Siemens (software development).
Rotterdam collaboration
The collaborators considered a total of 30 marine parts as to suitability for AM/3DP, and seven were selected as affording the best possibilities for this type of production: an exhaust gas manifold; a turbocharger nozzle ring; a MARIN-designed fixed pitch propeller; a Fokker-designed hinge; a box heat exchanger; a turbocharger gas inlet/outlet casing; and a Huisman-designed spacer ring.
From the pilot project, it emerged that the principal advantages of 3D printing were as follows:
- Reduced inventories for spare parts;
- Faster component production, reducing or obviating unscheduled vessel downtime;
- Reduced investments in tooling and other production-related costs for lightweight components;
- Reduced use of materials, and reduced weight, through optimised product design;
- Reduced logistic costs;
The ability to reproduce products by 3D scanning and reverse engineering if drawings of the originals are no longer available.
However, from the demonstrator cases of 3D printing of selected parts, the participants found it very difficult to make realistic comparisons between the cost of the 3DP process and conventional manufacturing.
As a direct consequence of the ‘3D Printing of Marine Spares’ endeavour, the Port of Rotterdam Authority and partner initiators InnovationQuarter and RDM Makerspace implemented a scheme to establish an Additive Manufacturing Fieldlab at the latter’s Innovation Dock premises in the port. Following the completion of the pilot scheme, the second phase of the project is a joint industry collaboration entitled RAMLAB, to produce certified metal parts on demand, using the wire arc additive manufacturing process.
According to the RAMLAB partners, wire arc AM technology offers various technical advantages, with fewer safety and operational issues, in relation to other, comparable AM systems. The metal parts produced will be salient to the maritime, industrial, aeronautical and other sectors. So far, 15 companies have declared interest in participating in the second stage.
Diverse trials
In the USA, naval shipbuilders have implemented 3DP for the printing of parts as well as for modelling and prototyping. An AM laboratory was opened at the Carderock Division of the Naval Surface Warfare Center (NSWC) in March this year, with the primary aim of promoting knowledge and exposure to the technology among NSWC employees.
The China Shipbuilding Industry Corporation (CSIC) has put three years’ work so far into acquiring the know-how, skills and means of using 3DP. An important juncture in its R&D efforts was signalled by tests with the use of the direct metal laser sintering (DMLS) technique, carried out by the CSIC 705th Research Institute.
3DP is being used by the Hamburg Ship Model Basin (HSVA) and also by UK research company QinetiQ in Portsmouth to manufacture prototype ship model components. According to Stratasys, its 3D printer has enabled the Hamburg test tank and research centre to reduce production lead times for prototype model parts by 70% and cut costs by 30%. It is claimed that the resulting plastic components meet the requisite standards of quality, precision, and durability. Moreover, 3DP confers greater flexibility to respond to last-minute customer requests and specification changes.
It is acknowledged throughout industry that 3DP is still an expensive technology. But the unerring advance in 3D printer design and performance, achieving increasing build rates by adding extra lasers, coupled with higher power, accuracy and quality control while printing, raises the work value of the tools. Companies and organisations prepared to put the resources into gearing up with the technology now, and accepting that the payback will take time, should have a competitive edge in the future.